Candu Tooling
UniTech decontaminates and demobilizes 2.5 million lbs. of tooling
Summary
UniTech decontaminated and demobilized 2.5 million lbs. of mid-cycle refurbishment tooling from Candu Energy’s (AtkinsRéalis) Candu 6 reactor. To complete this project, UniTech revolutionized the industry practice of monitoring and decontamination, optimizing selection of radiation detectors, implementing new and customized decontamination processes, and enhancing in-house material handling capabilities.
The Challenge
When Candu Energy’s (AtkinsRéalis) mid-cycle refurbishment project was cancelled in 2013, Candu Energy was left with an obsolete tool set designed specifically for refurbishing Candu 6 nuclear reactors. This extensive mid-cycle refurbishment tooling set, weighing in at 2.5 million lbs. and requiring 715 containers, represented a liability that needed to be managed through final disposition.
The Solution: Advanced Monitoring Techniques
For Candu, UniTech engineered and implemented new radiation monitoring techniques to process over 70 shipments of Candu’s tool set.
New Hand Frisking Techniques
The Candu 6 tool demobilization project includes components of many diverse, even one-of-a-kind, shapes with substantial material weight. The dynamic factor of unique, heavy components demanded hand frisking for a major portion of survey work.
UniTech engineered a new series of fixed-surface hand frisking jigs, called MJM Beta Jigs, using electronics from its Automated Laundry Monitor and breaking the channels into groups. These new detectors were built to ensure optimum monitoring for heavy and odd-shaped items. MJM Beta Jigs minimize human error complications prevalent in traditional hand frisking methods.
With the majority of a 2.5 million-lb. tool set requiring hand frisking, new hand frisking technology was crucial to completing monitoring tasks efficiently and affordably for the customer.
Custom automated monitoring systems
UniTech has also designed and used custom monitors throughout the Candu project to ensure that its customer receives consistent, reliable, repeatable monitoring results.
In the Candu project, UniTech employed a pipe monitor that uses overlapping detectors positioned around the pipe. The Pipe Monitor then completely rotates the pipe ensuring that the exterior surfaces are completely monitored, no matter how unique the geometry. The 2,500 dpm/100cm2 at a 95-percent confidence level for Cs‐137 point source geometry achieved by the pipe monitor’s survey cannot be duplicated with handheld detectors.
UniTech’s Internal Surface Monitor, featuring a 42-inch-by-2-inch detector (featuring a 500 cm2 active area) capable of monitoring inside of pipes with a diameter between 4 inches and 24 inches, was also used.
The Solution: Custom Decontamination Processes
With 2.5 million lbs. of oddly-shaped, unconventional units of tooling and equipment to decontaminate, UniTech’s diverse arsenal of custom methods has assured any and all Candu tooling can be properly decontaminated. UniTech’s decontamination methods include:
- High-pressure washing with surfactants
- Low pressure steam & chemical pre-soak
- CO2 dry ice
- Multimedia
- Aluminum oxide
- Walnut shells
- HEPA-controlled and precise manual decontamination
The Solution: Enhanced Material Handling Capabilities
UniTech’s licenses and material handling capabilities were pertinent to addressing the sheer size of the Candu 6 tool demobilization project. Firstly, completion of this Canadian project required a proper Waste Nuclear Substance License and Emergency Response Assistance Plan on the Canadian side of the border to allow management and export.
UniTech’s U.S. regional facilities are licensed to accept tools, equipment and waste materials from Canadian customers, then monitor, decontaminate, and, as needed, ship contaminated materials to UniTech’s newly acquired ORSC facility for final disposition, including BSFR at reduced rates.
UniTech handled Candu’s tools at its Morris, Illinois radioactive material processing facility, which provides low, stable backgrounds; ample space; a focused labor group; and high-tech instrumentation for technically superior and cost-effective services. Throughout the Candu 6 demobilization project, much disassembly of equipment has been required before monitoring and decontamination could take place. Disassembling in UniTech’s off-site, spacious facilities was ideal for completing this massive task.
The Results
With a BSFR license, UniTech has the capacity to take on “problem” projects with which nuclear facilities had previously been burdened. The license has also enabled UniTech to develop a fleet-wide tool and equipment management program that will minimize liability and responsibility of outage materials needed for recurring use.
UniTech’s off-site monitoring and decontamination methods minimize liability. 2.5 million lbs. of obsolete tooling and equipment is quite the burden for a nuclear facility to handle. By partnering with UniTech, Candu’s unique needs were met with custom solutions offering reduce risk and liability.
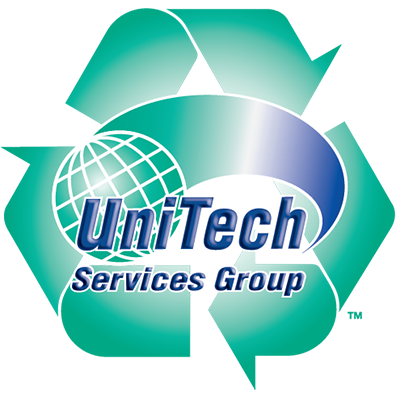
Copyright © 2024 UniTech. All rights reserved. Privacy Policy